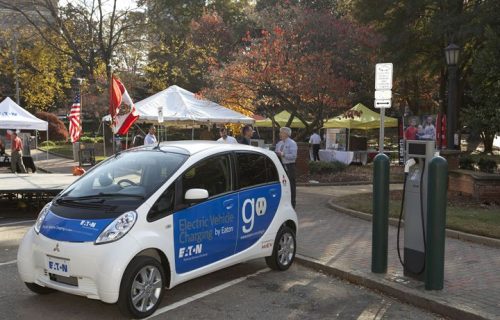
The Electric Car: Lighter, Less Costly, Plugged In
In writing “The Electric Car, Unplugged” for the New York Times of Sunday, March 25, John Broder and his informants assert that “enthusiasm over electrification in the industry has begun to flicker and the price of battery technology remains stubbornly high.” Yet they unaccountably omit the most promising way to make electrified autos rapidly affordable: use ultralight materials like carbon-fiber composites, and new manufacturing techniques to make them into automotive structures, to produce integratively designed tripled-efficiency autos. Their “fitness”—losing a ton of weight while improving aerodynamics and tires— saves up to two-thirds of the batteries or fuel cells otherwise required. Making those costly components fewer before making them cheaper makes electric autos affordable, so their higher sales make their components cheaper.
This reversal of traditional industry and government priorities engages three steep learning curves (making more lowers the cost)—in ultralight materials, structural manufacturing, and electric powertrain—that together create a breakthrough competitive strategy. Surprisingly, the smaller powertrain plus the carbon-fiber autobodies’ radically simplified manufacturing, requiring only one-fifth the traditional amount of capital, pays for the carbon fiber, making ultralighting free. That is, such ultralight carbon-fiber cars cost no more to manufacture than today’s steel autos, but their higher value makes them more profitable to make and sell.
Our team and its industry partners designed an uncompromised, 52-percent-lighter carbon-fiber SUV in 2000 getting 67 mpg on gasoline or 114 on hydrogen fuel cells, repaying its extra cost (due to its powertrain, not the ultralighting) in a year or two. Toyota showed a concept carbon-fiber plug-in hybrid in 2007 with the interior volume of a Prius but one-third its weight—the day after the world’s biggest carbon-fiber maker announced a $0.3-billion factory to “mass-produce carbon-fiber car parts for Toyota.” Now VW, BMW, and Audi have announced volume production of the first three electrified carbon-fiber autos by next year. VW’s offering, the two-seat XL-1 plug-in hybrid, is rated at 230 miles per gallon of gasoline equivalent. Up to four other automakers are quietly moving toward a similar strategy.
Other efforts are under way to build momentum. The University of Michigan’s Center for Automotive Research this year launched the Coalition of Automotive Lightweighting Materials to support efforts by auto manufacturers to cut vehicle weight. The coalition includes materials associations for aluminum and plastics, along with several auto suppliers. Finally, President Obama last week announced a $14.2 million Energy Department effort to accelerate the development and deployment of stronger and lighter materials for advanced vehicles.
The potential for automotive lightweighting is described and documented in Rocky Mountain Institute’s October 2011 business book Reinventing Fire: Bold Business Solutions for the New Energy Era, and summarized in my article in the March/April issue of Foreign Affairs. The attitudes Broder reports do reflect automakers’ old conventional wisdom, but thankfully, not the industry’s most advanced strategies and activities, as will soon become evident in the marketplace.